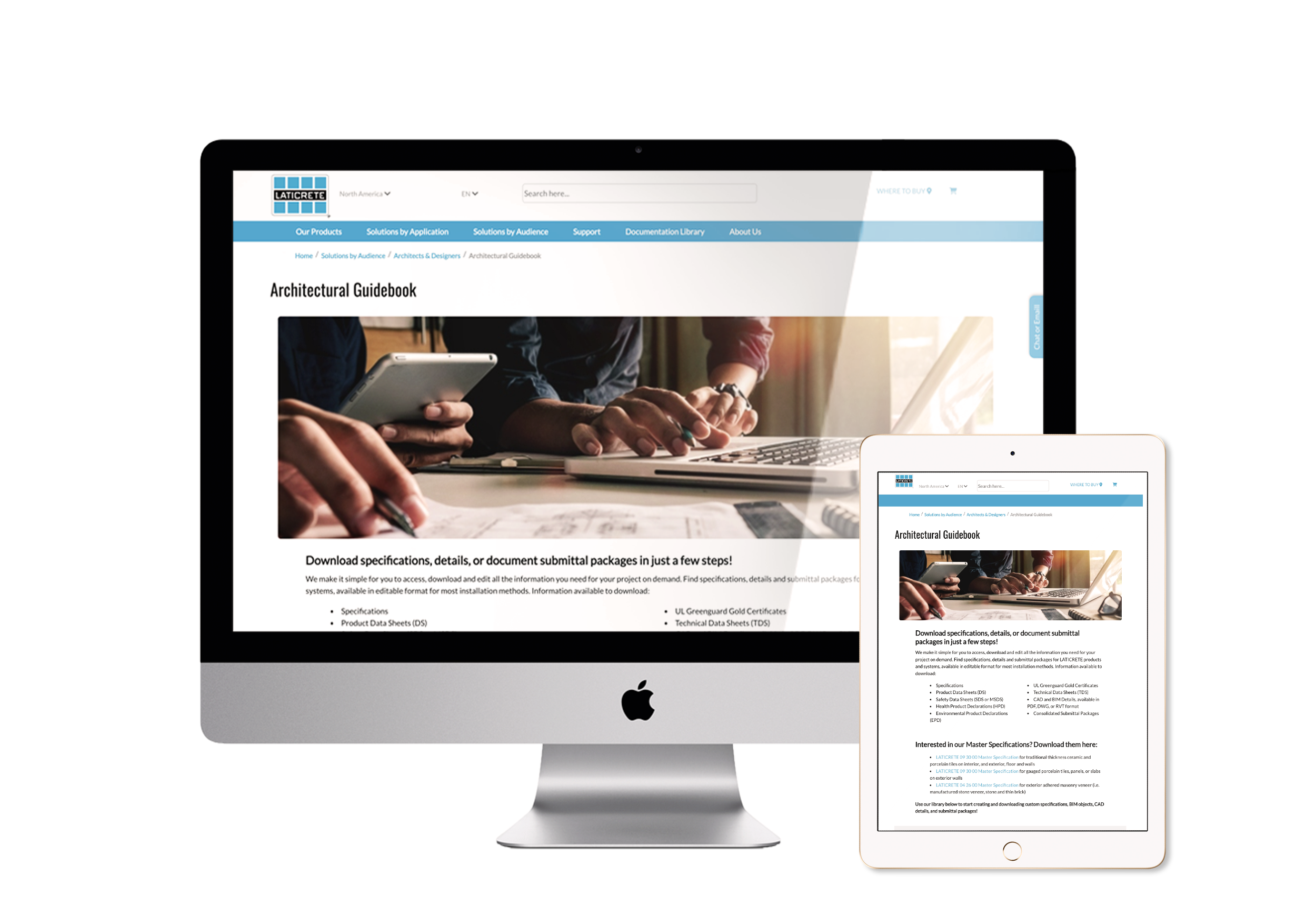
Get support when you need it, 24/7.
Get the resources and support you need with the industry's most comprehensive technical support program. With online resources, you get answers to the most frequently asked questions from the LATICRETE team. Search FAQs on how to plan or troubleshoot your job organized by product category.
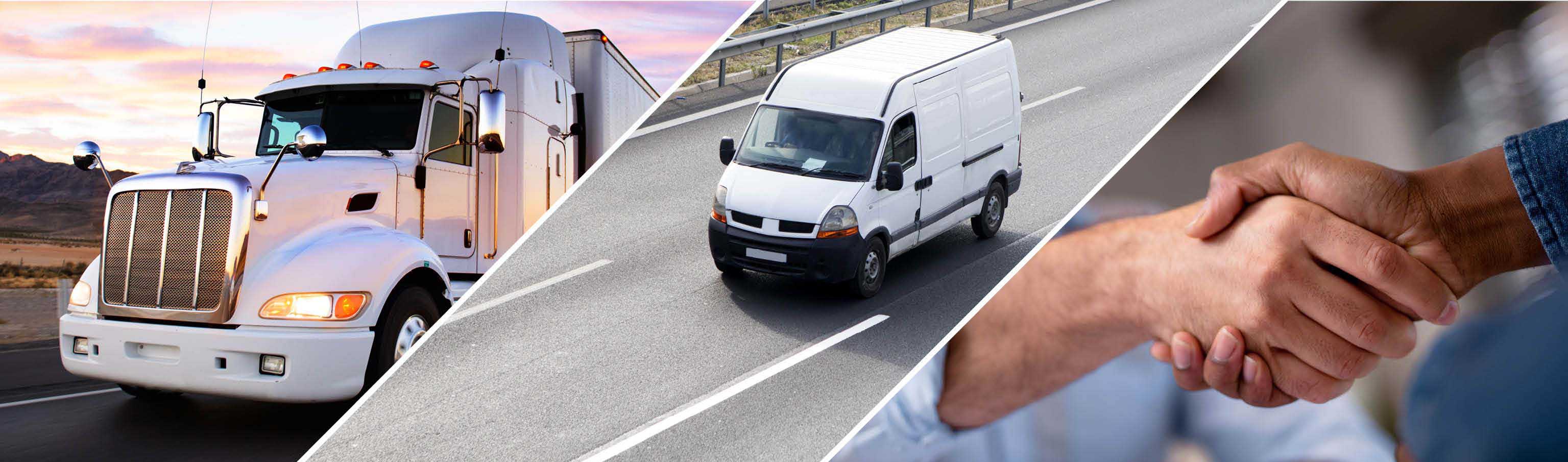
Distributor FAQs: Transportation Management System (TMS)
Have a specific question about our TMS? Looking for more information on shipping and tracking confirmation? Your question may have already been asked and answered.
Whether you're wondering about orders, full truckloads, LTL or cancellations and changes, our team has an answer for you.